DFD6361
Fully Automatic Dicing Saw
Advanced performance for Φ300 mm dicing
• Φ300 mm • Facing dual spindle • DBG
Enhanced dicing throughput
The DFD6361 enhances throughput in two distinct ways. DISCO’s facing dual design and a reduction in the distance between the blades help to control total cut time, while high-magnification microscopes (standard) and non-contact setup sensors (option) for both Z1 and Z2 reduce the time required for non-dicing sequences, such as kerf check and blade setup.
Consistent cut quality
DFD6361 offers highly consistent and dependable cut quality through the new Synchro Spindle™ featuring superior radial rigidity. An atomizing nozzle cleaning mechanism can also be installed in the spinner unit as an option to effectively clean wafers after dicing (Patent no.3410385).
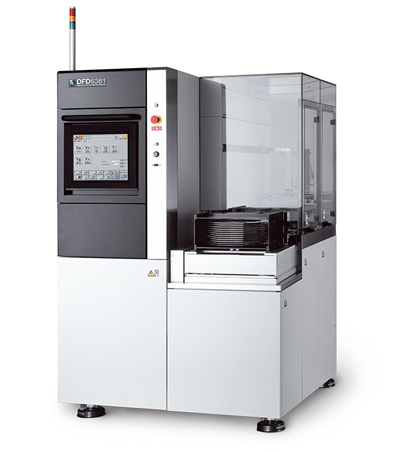
Improved usability
Spindle lineup
Small footprint
DFD6340 Operation flow
- Frame pick arm moves the workpiece from the cassette to the pre-alignment stage →
- After centering on the pre-alignment stage, the lower arm moves the workpiece to the chuck table → cutting →
- Upper arm moves the workpiece to the spinner table → cleaning and drying →
- Lower arm moves the workpiece to the pre-alignment stage →
- Frame pick arm returns the workpiece to the cassette
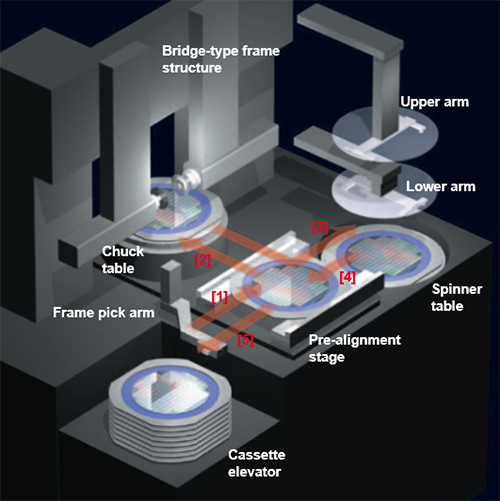